Blog
Industria 4.0
KPI di produzione: stati di un impianto secondo l’approccio OEE
Webmaster
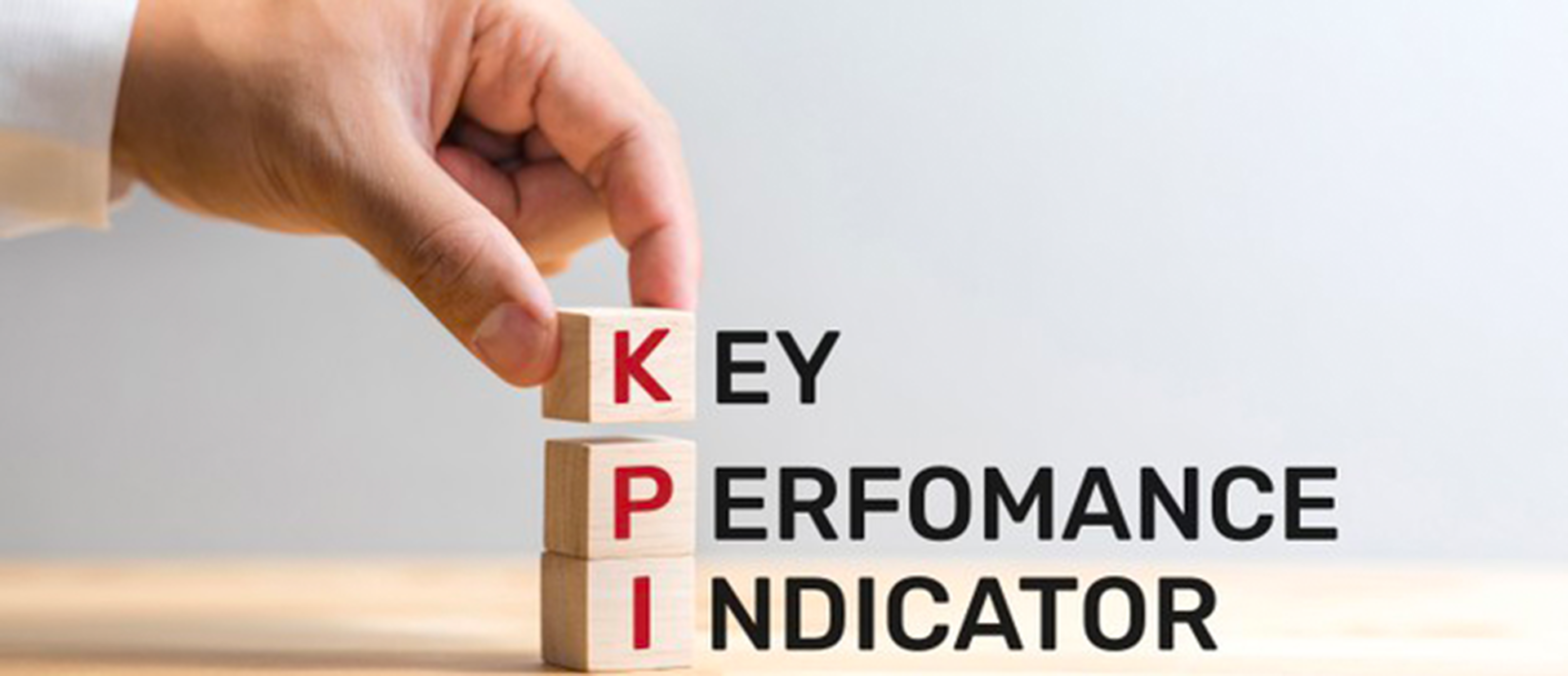
Quando si parla di misurazione dei KPI di produzione (Key Performance Indicator) si fa riferimento a indicatori oggettivi, quantitativi, in grado di misurare le prestazioni di un impianto.
Ma per avere un quadro esaustivo dal quale partire per individuare i KPI più idonei, è necessario fare un passo indietro ed analizzare le condizioni operative. Queste rappresentano infatti l’essenza vera a propria di un sistema produttivo e la loro progressiva ottimizzazione comporta un progressivo miglioramento delle performance di produzione.
Facendo un ulteriore passo indietro, prima di approfondire le modalità di calcolo delle condizioni operative di un impianto di produzione, è necessario conoscere esattamente gli stati in cui possono trovarsi le risorse che lo caratterizzano. Per fare questa analisi partiamo dall’assunto che T rappresenta il tempo di apertura di un impianto ed è segmento di Ts, ovvero del tempo solare.
Possibili stati di un impianto
Oltre a T e a Ts in un impianto è possibile individuare molti altri tempi utili per misurare le performance di produzione:
- TPb: tempo di produzione dei pezzi buoni, che superano il primo controllo qualità ;
- TPs: tempi di produzione dei pezzi di scarto;
- TPr: tempo di produzione di campionature o pezzi di prova;
- TG: tempo di mancato funzionamento a causa di guasti (manutenzione non programmata);
- TM: tempo di mancato funzionamento per la manutenzione programmata;
- TS: tempo di mancato funzionamento per set up;
- TMo: tempo di mancato funzionamento per mancanza di ordini (per esempio se si considerano produzioni stagionali);
- TMm: tempo di mancato funzionamento per mancanza di materiali;
- TO: tempo di mancato funzionamento per cause organizzative;
- TSc: tempo di mancato funzionamento per cause sindacali;
- POT:Plan Operating Time, ovvero il tempo in cui l’impianto è aperto e teoricamente disponibile a produrre. Il POT si ottiene sottraendo TSc da T.
Secondo questa prima impostazione il tempo effettivo di produzione equivale al tempo impiegato per la realizzazione di pezzi buoni, di scarto e al tempo di set up. Quest’ultimo, infatti, in molte realtà produttive è considerato tempo standard, poichè necessario per la produzione per esempio in realtà multiprodotto.
Nell’immagine che segue abbiamo rappresentato graficamente i vari tempi di un impianto analizzati secondo la logica appena presentata, che tiene conto di cause tecnologiche, gestionali e organizzative.
Gli stati di un impianto nell’approccio OEE (Overall Equipment Effectiveness)
L’approccio basato sull’OEE, al contrario del precedente, tende a raggruppare gli stati di un impianto in due macrocategorie: fermi per cause pianificabili o non panificabili. Per esempio, in questo caso, i set up sono considerati perdite di tempo operativo. Il management aziendale, pertanto, sarà concentrato nel tentare di ridurli e razionalizzarli al massimo.
Nell’immagine qui sotto sono riportati gli stati di un impianto secondo la logica dell’OEE.
Verso l’approccio standardizzato
Le due modalità di analisi degli stati di un impianto proposte, rappresentano convenzioni basate su differenti modelli di produzione. Questo significa che non vogliono indicare una soluzione giusta e sbagliata. C’è però da sottolineare che l’analisi dei tempi e delle causali di fermo di un impianto basata sull’approccio dell’OEE sembra andare verso la standardizzazione soprattutto per le realtà vicine ai modelli di lean production.
In particolare, se si decide di addentrarsi nell’analisi delle causali di fermo di un impianto, è importante comprendere fin da subito che una catalogazione molto dettagliata è molto più funzionale di una catalogazione approssimativa. Allo stesso modo, per supportare gli operatori nelle compilazione delle causali, è opportuno non procedere ad una decodifica troppo articolata perchè potrebbe tradursi in dichiarazioni poco attendibili.
Il ruolo del software MES per l’analisi delle causali
Un valido strumento da implementare all’interno del plant produttivo per facilitare la raccolta delle causali dei fermi e l’analisi delle performance è il software MES (Manufacturing Execution System). Attraverso tale sistema infatti, è possibile raccogliere in maniera automatizzata le informazioni di interesse provenienti dalle macchine in produzione. Tempi per la produzione di pezzi buoni, tempi per l’approvvigionamento, calcolo dell’OEE e molte altre informazioni, diventano velocemente consultabili dai plant manager e responsabili di produzione che possono così usufruire di un ottimo strumento per il decision making.